ANA Engine Technics and CareAR
– Enhancing Efficiency and Quality in Aircraft Maintenance
We recently helped our client ANA Engine Technics to implement CareAR.
Why did they choose this transformative product, and how did it help them?
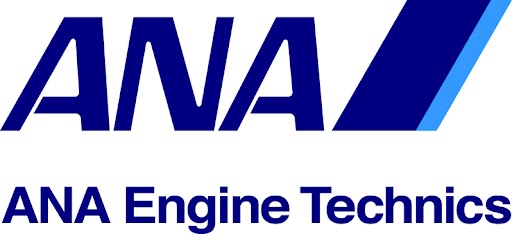
Challenges Before CareAR
-
Frequent Travel
We wanted to reduce the amount of travel between maintenance sites and offices, as well as to overseas locations
-
Limitations of Video Conferencing
We found it hard to use conventional video call solutions for maintenance activities. These are simply not designed for showing specific parts of equipment and discussing areas that need attention or adjustments
-
Time to Recovery
It took a long to time communicate with equipment manufacturers when an issue happened. This lengthened the time to recover.
How CareAR Helped
-
Efficiency Gains
We were able to significantly reduce travel time between sites. Some tasks that previously needed an in-person presence can now be managed remotely.
-
Quality Improvement
By using CareAR’s annotation and laser pointer tools we can have precise and easy communication of visual details. This improved the quality of maintenance work.
-
Faster Recovery
The ability to collaborate in real-time sped up recovery times, reducing system downtime and enabling quicker recovery.
Tell us more about the challenges you faced
We have always worked hard to improve the quality of engine maintenance work. At the same time, we try to reduce the needed hours to be as efficient as we can be. However, it can be hard to meet both these goals at the same time.
Let’s consider an example. A mechanic working on a remote site discovers a problem during maintenance. The mechanic needs to show the problem to our staff at one of our main locations. In the past, this often required a visit to the site.
Aircraft engine maintenance requires a high level of skill and training. This means that certain problems often require help from a specialized mechanic. This also often required trips to the site, no matter how far away it was. And this had to be done on short notice, as many issues are urgent.
As a result of the covid-19 pandemic, our staff started to use remote communication tools. We continued to implement such tools and try to use them to support remote mechanics. However, the normal options for video conferencing were difficult to use in a maintenance situation. Our staff tried to use gestures and figure pointing to show the issues and discuss them. But this simply didn’t work as well as in-person discussions.
How did CareAR help you?
Since CBA has helped us to implement CareAR, in-house staff have been able to help mechanics without having to go to the site each time. They are also able to share the situation with a larger number of skilled mechanics. This has improved the quality of the work while also reducing hours.
Unlike traditional video calling tools, CareAR has an annotation and laser point function. These features have helped those in a call to show the specific part and issue, with complete clarity. In other words, they resolved the problems we had with traditional conferencing tools. We also found that these tools helped us improve the quality of the maintenance.
With CareAR, we have also been able to improve our response time. Many issues are urgent, and in the past, we often had to send specialized mechanics to provide support in person. This delayed the repair and often needed overseas travel.
With CareAR, we estimate that we save at least 400 hours of skilled labor per year.
What was the deciding factor for you in choosing CareAR?
What features of CareAR do you find are easy to use?
We really appreciate the annotation features, as well as the laser pointer function. Even if the camera moves, the annotation stays fixed on its location.
The design of the app is simple and easy to use as well. Even first-time users can use it intuitively, without extensive training. Even our veteran engineers regard it highly.
Unlike conventional video conferencing tools, CareAR is focused on fieldwork. We appreciate how well it has worked as a purpose-built tool for this situation. For example, as soon as a session is started, CareAR shows the scene from the external camera, rather than the from the selfie camera. This saves a click each time. Similarly, for those connecting remotely, they at once see the view of the equipment instead of the person. These may seem like small things, but they are very important in field operations where speed is vital.
Please tell us what you find convenient about CareAR
We like the fact that it is possible to join a session with just the web browser, if needed. This makes it convenient for those who do not yet have the app installed to join.
The ability to include an unlimited number of users is also helpful. We often have many departments involved in airplane engine maintenance. For example, flight operations, production control, technical personnel, and field technicians often all must meet at the same time. CareAR makes it easy to bring all these together just by sharing the URL of the meeting with a key person in each department, who can forward it to others.
Can CareAR help in an emergency?
Yes. When a malfunction happens with an engine, it can help us to recover quickly.
In the past, if a problem happened with a testing device or repair tool, a mechanic first tried to fix an issue. While the equipment manual was helpful in doing so, it was often not enough. This meant contacting the manufacturer and waiting for them to help. During this time, work that required that tool or testing device was stopped. This affected the maintenance schedule.
With CareAR, however, the mechanic can at once show the problem to the manufacturer. They can troubleshoot together, leading to quick repairs and reduced downtime. This also reduces the number of times specialist personnel must come to a site to repair equipment.
Do you have a recent example of such an early recovery?
We had a large piece of equipment used for machining breakdown. It was several meters long. Our mechanics were able to use CareAR to contact the manufacturer in Europe.
We used CareAR to connect staff from the equipment manufacturer in Europe, our Japan office, and at the site of the issue. By using CareAR, all involved could clearly see the equipment with the problem. Our on-site staff were even able to put the camera inside the machine to show how it worked. Then they could act according to the engineer’s instructions in testing how the machine moved. Through this real-time collaboration, we were able to find and solve the issue quickly. The equipment manufacturer also spoke highly of CareAR, commenting that “it’s very good to be able to see it together.”
When meeting with multiple locations, spread across time zones, it is difficult to schedule a time that works for all. However, with CareAR we can share and resolve the situation in a single meeting. This eliminated the need to find a good time for a follow-up meeting. We also saw that the use of visual annotations helped with the language barrier.
What are your future plans for CareAR?
We will continue to use CareAR as we have been, as well as look for more areas to expand its use. The benefits of this tool are clear even in early use, so we expect this will continue.
At this time, we want to share our appreciation of CBA and your partner CareAR for your help in this implementation. We look forward to future collaboration together.